一技術背景和研發(fā)思路
繼京都議定書、巴黎氣候峰會之后,2020年中國政府在聯(lián)合國大會和氣候雄心峰會上莊嚴承諾“二氧化碳排放力爭2030年前達到峰值,努力爭取2060年前實現(xiàn)碳中和”。據(jù)統(tǒng)計,我國鋼鐵生產(chǎn)每年排放CO2超過19.6億噸,占全國溫室氣體總排放的15%左右,減少鋼鐵生產(chǎn)CO2排放,尋求CO2在鋼鐵流程內(nèi)的規(guī)?;晕蚁緩?,是我國早日建成“碳中和”國家,切實踐行“大國承諾”的重要助力。
我國處于由高速增長邁向高質(zhì)量發(fā)展轉變的關鍵時期,技術創(chuàng)新是實現(xiàn)高質(zhì)量發(fā)展的強大動能。如何解決鋼鐵生產(chǎn)污染物排放問題,并提供高品質(zhì)的鋼鐵產(chǎn)品,是我國鋼鐵工業(yè)實現(xiàn)行業(yè)轉型升級的核心命題。我國煉鋼工序每年產(chǎn)生超過2000萬噸的煉鋼煙塵。廣泛采用的煉鋼煙塵后處理方式能耗高,難度大,給企業(yè)帶來巨大的負擔;煉鋼煙塵中的微細顆粒難以通過除塵系統(tǒng)除凈,成為加重霧霾產(chǎn)生的因素之一。如何從源頭上減少煉鋼煙塵,實現(xiàn)其源頭抑制是亟待破解的世界難題。
隨著社會高質(zhì)量發(fā)展對鋼鐵材料品質(zhì)需求的持續(xù)提高,磷、氮、氧的深度脫除及潔凈化精準控制,越來越成為高質(zhì)量鋼鐵產(chǎn)品生產(chǎn)的技術難題。轉爐作為鋼鐵生產(chǎn)流程的核心裝備,亟需跨越式的技術變革。冶煉前期硅、錳、碳等的劇烈氧化反應放熱帶來的熔池快速無序升溫,破壞了高效脫磷的“低溫”熱力學條件,造成深度脫磷困難,雙渣法或雙聯(lián)法雖在一定程度上解決了煉鋼脫磷的問題,但也帶來了煉鋼渣量和成本的增加;底吹Ar氣泡脫氮能力不足,無法保證超低氮鋼的穩(wěn)定生產(chǎn);冶煉末期,熔池失去了CO氣泡的攪拌效益,鋼水氧含量往往超過500ppm,我國每年脫氧劑消耗折合成鋁約40萬噸,脫氧產(chǎn)物帶來的大量夾雜物易成為鋼鐵質(zhì)量缺陷,后續(xù)精煉負擔重、能耗高。
轉爐復吹煉鋼工藝能在一定程度上改善熔池的反應動力學條件,有利于鋼水脫磷、脫氮、控氧,減少終點鋼水過氧化和渣量消耗。但由于底吹大流量強攪拌和透氣元件長壽之間的矛盾一直無法調(diào)和,煉鋼爐底吹使用壽命無法與爐齡同步,安全風險長期存在,嚴重影響了底吹氣體攪拌效益的發(fā)揮。
2004年起,項目團隊依托國家科技支撐計劃、國家自然科學基金重點及面上項目的持續(xù)支持,以CO2利用、固廢減量、鋼質(zhì)潔凈、降本增效為目標,開發(fā)了二氧化碳利用于煉鋼工藝的原創(chuàng)技術,發(fā)現(xiàn)并掌握了CO2具有的反應冷卻、氣泡增殖、弱氧化、強沖擊等獨有特性,實現(xiàn)了CO2利用和煉鋼生產(chǎn)工藝的完美結合,解決了煉鋼脫磷、脫氮、控氧和底吹長壽等諸多煉鋼工藝難題,開辟了煉鋼過程CO2規(guī)?;{利用路徑。
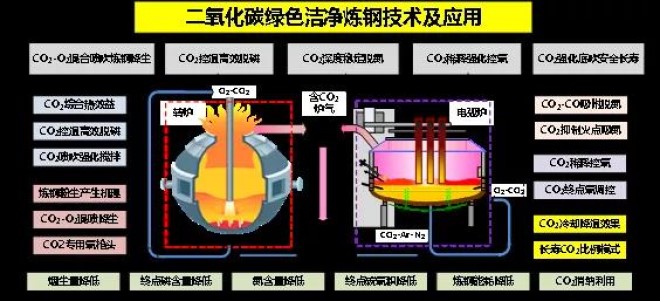
二氧化碳綠色潔凈煉鋼技術及應用
二主要創(chuàng)新內(nèi)容
項目團隊提出了“二氧化碳綠色潔凈煉鋼技術及應用”項目,從煉鋼過程抑制煙塵、高效脫磷、穩(wěn)定脫氮、強化控氧和底吹長壽等方面入手,解決了煉鋼煙塵和爐渣固廢源頭減量,鋼水磷、氮、氧潔凈控制的諸多煉鋼工藝難題,先后發(fā)明了CO2-O2混合噴吹煉鋼降塵技術、CO2控溫高效脫磷技術、CO2吸附深度穩(wěn)定脫氮技術、CO2稀釋強化控氧技術和CO2強化底吹安全長壽成套技術,實現(xiàn)了煉鋼過程節(jié)能減排、鋼質(zhì)潔凈、降本增效的目標。具體創(chuàng)新內(nèi)容如下:
1.CO2-O2混合頂吹煉鋼降塵技術
煉鋼每生產(chǎn)1噸合格鋼水產(chǎn)生約20-30kg煙塵,按我國2019年鋼產(chǎn)量9.96億噸計,煙塵量達2000-3000萬噸,尤其是煉鋼煙塵中的微細粉塵難以通過除塵系統(tǒng)除凈,成為霧霾產(chǎn)生的因素之一。我國煉鋼煙氣除塵后處理方式,每年耗能高達90億kgce,并額外增加CO2排放2250萬噸。煉鋼煙塵通常含有較高有毒有害物質(zhì),難以通過循環(huán)方法加以處理利用;采用堆放或填埋方式,造成資源浪費,并可能向土壤轉移甚至發(fā)生重金屬污染。從源頭上抑制煉鋼煙塵的產(chǎn)生將具有重大的經(jīng)濟效益和環(huán)境意義。
項目團隊揭示了煉鋼煙塵的產(chǎn)生機理和變化規(guī)律,探明了轉爐煙塵的“蒸發(fā)-氣泡”混合作用產(chǎn)生機制,確認高溫火點鐵蒸發(fā)是煙塵產(chǎn)生的主要原因,占煙塵總量的70-80%。首次提出降低火點區(qū)溫度有效控制鐵蒸發(fā)的思路,將CO2氣體用于煉鋼過程降低煙塵產(chǎn)生,發(fā)明了轉爐CO2-O2混合噴吹煉鋼降塵技術,配套研制了CO2-O2混合噴吹系統(tǒng)及裝置,制定了鋼鐵行業(yè)CO2-O2氣體混合利用標準。穩(wěn)定控制了火點區(qū)溫度低于鐵的沸點(2750℃),減少煉鋼煙塵產(chǎn)生,將煉鋼煙塵由完全依靠后處理轉變?yōu)榍耙种?,打破了煉鋼煙塵傳統(tǒng)治理的方式。
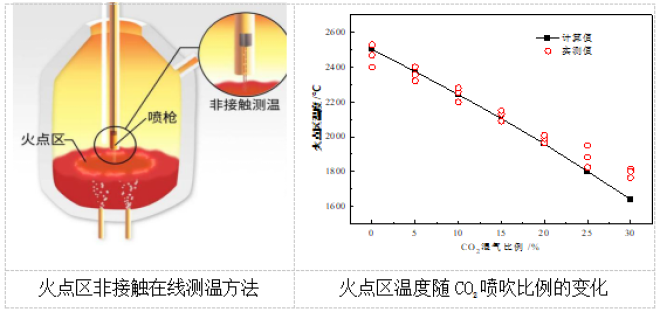
完成了CO2資源化應用于300t轉爐的國家示范工程,實現(xiàn)了CO2-O2混合頂吹煉鋼降塵技術的應用及推廣。實現(xiàn)煉鋼煙塵源頭減量9.95%,煙塵中Fe降低12.98%,鋼鐵料節(jié)約4.09kg/t,噸鋼煤氣增產(chǎn)5.57Nm3,煤氣中CO濃度提高3.73%,驗證了CO2-O2混合噴吹降低煉鋼煙塵產(chǎn)生的工業(yè)應用效果。
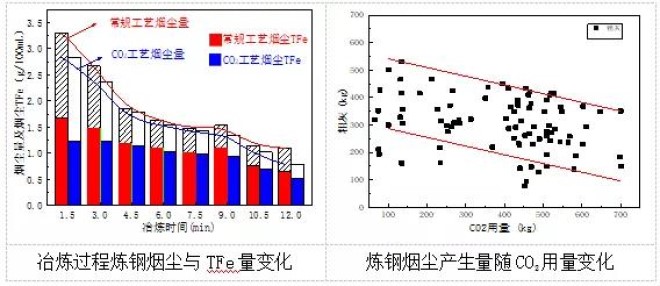
2.CO2控溫高效脫磷技術
脫磷是煉鋼最重要任務之一,是冶煉高品質(zhì)鋼的技術難點。隨著低磷及超低磷鋼品種需求的增加,對煉鋼脫磷提出了更高要求。轉爐冶煉中硅、錳、碳等的劇烈氧化反應放熱帶來的熔池快速無序升溫,破壞了高效脫磷的“低溫”熱力學條件,同時鋼渣攪拌動力不足,造成終點磷含量偏高,深度脫磷困難。雙渣法或雙聯(lián)法雖在一定程度上解決了煉鋼脫磷的問題,但易受節(jié)奏及工藝條件等諸多限制,也帶來了煉鋼渣量和成本增加。
項目團隊探明了CO2噴吹減緩熔池升溫和強化熔池攪拌的作用規(guī)律,發(fā)現(xiàn)CO2-O2混合頂吹可延長最佳脫磷溫度時間20%、增加射流沖擊面積36%,發(fā)明了CO2-O2混合頂吹熔池“升溫-控溫”熱平衡模型和CO2比例分段動態(tài)調(diào)控技術,制定了轉爐頂吹CO2用于脫磷的工藝標準,建立了適應不同鋼種的雙聯(lián)脫磷模式及階梯式脫磷方法,保證了CO2控溫高效脫磷,突破了長期困擾煉鋼深脫磷的技術瓶頸。
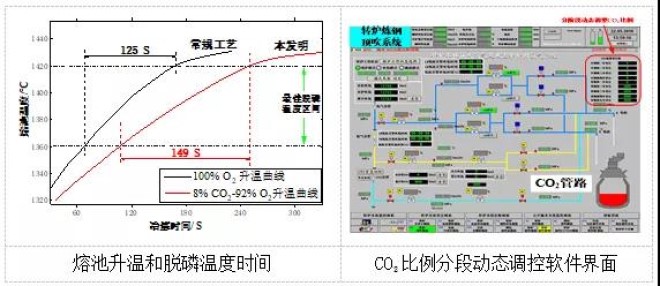
本創(chuàng)新技術先后在首鋼京唐鋼鐵聯(lián)合有限責任公司、福建三鋼閩光股份有限公司成功投入工業(yè)應用,保障了超低磷鋼穩(wěn)定生產(chǎn)。首鋼京唐半鋼脫磷轉爐脫磷率提高6.99%,常規(guī)轉爐終點磷平均降至0.006%,實現(xiàn)噸鋼渣量減少7.8kg、石灰消耗減少1.5kg。
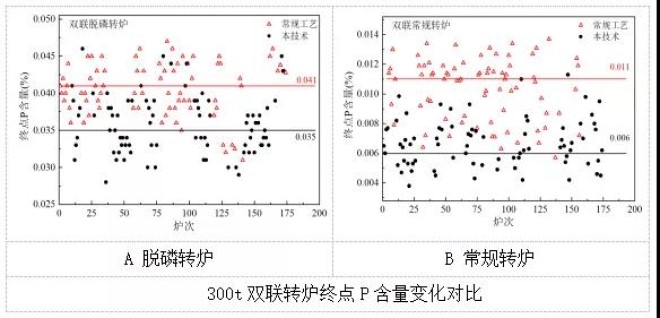
3.CO2吸附深度穩(wěn)定脫氮技術
鋼水中氮的深度脫除和穩(wěn)定控制是生產(chǎn)高品質(zhì)鋼的技術瓶頸。高端汽車板等要求成品鋼氮含量低于20ppm,由于Ar氣泡脫氮能力不足和冶煉后期CO氣泡數(shù)量有限,多數(shù)轉爐穩(wěn)定脫氮極限約在17ppm,無法保證超低氮鋼穩(wěn)定生產(chǎn),成為我國高端制造業(yè)金屬材料的“卡脖子”環(huán)節(jié)。
項目團隊系統(tǒng)研究了CO2、Ar、N2氣泡在鋼液內(nèi)的上浮運動和轉變規(guī)律,發(fā)現(xiàn)CO2-CO氣泡有利于打破氮原子傳質(zhì)的界面阻礙,脫氮表觀速率常數(shù)是Ar的9.6倍,CO2反應生成CO是O2的2.3倍,增量的CO氣泡成為鋼液脫氮的重要動力。獨創(chuàng)了煉鋼過程噴吹CO2吸附深度穩(wěn)定脫氮技術,開發(fā)了CO2-Ar動態(tài)底吹裝備系統(tǒng)及工藝控制模型,實現(xiàn)了鋼中氮的高效穩(wěn)定脫除,是高品質(zhì)鋼潔凈化生產(chǎn)技術的重要創(chuàng)新。
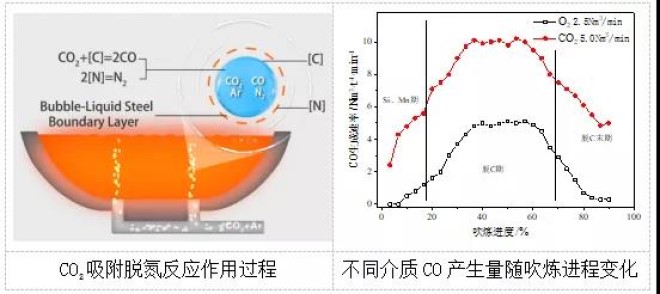
本創(chuàng)新技術在首鋼京唐鋼鐵聯(lián)合有限責任公司完成了工業(yè)應用,取得了良好的穩(wěn)定控氮效果,轉爐出鋼氮含量從17ppm穩(wěn)步降低至11ppm,氮含量波動幅度減小了35%,實現(xiàn)了高端汽車板用鋼的穩(wěn)定生產(chǎn)。創(chuàng)新技術推廣至天津鋼管制造有限公司、新余鋼鐵集團有限公司電弧爐應用。其中全廢鋼冶煉終點氮含量降低至43ppm,解決了長期以來電弧爐難以有效脫氮的難題,并以此為契機開發(fā)了高品質(zhì)低氮特鋼品種。
4.CO2稀釋強化控氧技術
抑制鋼水過氧化是煉鋼生產(chǎn)工藝的技術難點,尤其在接近冶煉終點時,鋼水C含量急劇減少后,熔池失去了CO氣泡的攪拌效益,只能單純依靠超音速射流的物理沖擊帶動熔池流動,造成鋼水過氧化嚴重。因金屬元素氧化,我國每年直接燒損鋼鐵料約3000萬噸,同時因脫氧采用脫氧劑需消耗鋁約40萬噸,且脫氧產(chǎn)物帶來的夾雜物易造成鋼鐵質(zhì)量缺陷。
項目團隊研究了CO2氣體的弱氧化稀釋作用和降低CO分壓的能力,掌握了頂吹CO2-O2射流的調(diào)控特性;熔池低碳條件下,CO分壓可降低21.5%,射流動能可提高8%。發(fā)明了轉爐CO2-O2混合頂吹稀釋強化氧調(diào)控技術及動態(tài)預報軟件,利用高比例CO2進行終點強攪拌,顯著減少了鋼液過氧化,是轉爐煉鋼終點控制方法的重要突破。
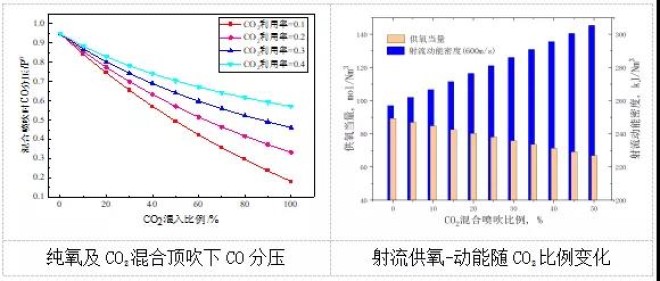
本創(chuàng)新技術在首鋼京唐鋼鐵聯(lián)合有限責任公司,取得了顯著降低鋼水過氧化的效果,轉爐終點碳氧積降至<0.0015,渣中TFe降低4.59%,對于超低碳汽車板等品種終點氧含量降低超過了100ppm。電弧爐煉鋼應用本技術后,冶煉終點平均碳氧積降低了3-5×10-4,推動了高品質(zhì)特鋼產(chǎn)品質(zhì)量提升。創(chuàng)新已甘肅酒鋼集團宏興鋼鐵股份有限公司多家企業(yè)應用。
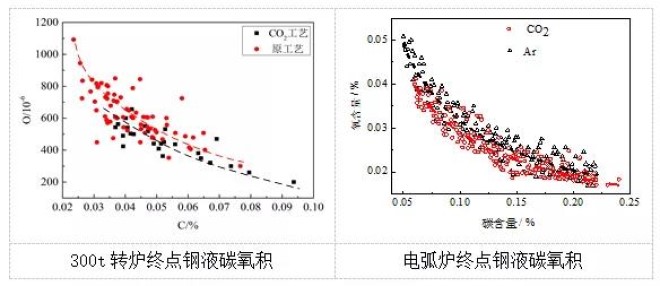
5.CO2強化底吹安全長壽成套技術
頂?shù)讖痛倒に嚹芨纳茻掍撊鄢氐姆磻獎恿W條件,有利于鋼水脫磷、脫氮、控氧,減少終點過氧化和渣量消耗,但因為底吹大流量攪拌和透氣元件長壽之間的矛盾一直無法調(diào)和,爐底壽命無法與爐齡同步,安全風險長期存在。企業(yè)只能采用小流量底吹維持元件壽命,嚴重影響了底吹氣體攪拌效益的發(fā)揮,甚至部分轉爐因安全考慮放棄使用底吹工藝,無奈接受煉鋼指標惡化的后果。如能在保證底吹攪拌強度的前提下,解決底吹元件的長壽問題,將帶來煉鋼工藝技術指標的全面提升。
項目團隊系統(tǒng)研究了煉鋼底吹元件的侵蝕機理,掌握了鎂碳耐材氧化脫碳規(guī)律和鋼液、氣泡機械侵蝕的作用行為。證實了底吹CO2具有很強的物理冷卻和化學吸熱作用,冷卻效果是Ar的10倍左右,發(fā)明了CO2-Ar動態(tài)切換及混合底吹工藝,利用CO2的物理-化學冷卻和增殖攪拌功能,解決了底吹元件的氧化侵蝕問題,實現(xiàn)了強攪拌下的底吹長壽,是煉鋼復合吹煉技術的重要突破。
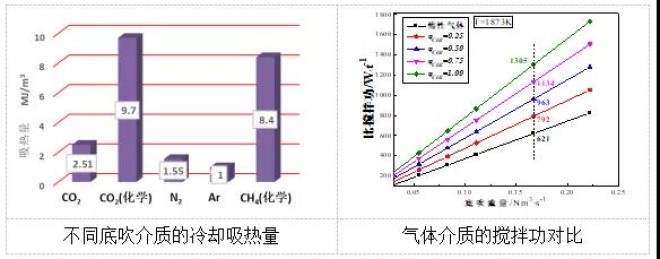
應用后轉爐底吹流量增加60%,攪拌強度提升2-3倍,有效底吹壽命延長50%,實現(xiàn)與爐齡同步,取得了良好的綜合冶金效益。
三項目應用和推廣情況
2016年,首鋼京唐鋼鐵公司300t雙聯(lián)轉爐完成了項目工業(yè)示范和國家驗收,建成了國內(nèi)外首套煉鋼專用“石灰窯尾氣回收CO2系統(tǒng)”工程,成功解決了“工業(yè)尾氣→CO2回收→煉鋼利用”流程中多項工程難題,形成了鋼鐵行業(yè)CO2循環(huán)利用標準(YB)體系,實現(xiàn)了CO2綠色潔凈煉鋼技術的集成應用。本項目工業(yè)應用后,各工藝合計CO2利用5.09Nm3/t,實現(xiàn)轉爐煉鋼煙塵產(chǎn)生量減少9.95%,石灰造渣材料消耗減少了1.5kg/t,爐渣TFe含量降低3.59%,爐渣減量7.8kg/t鋼,實現(xiàn)了煉鋼固廢的源頭抑制和綜合減量10.2kg/t,減輕了后處理壓力。使用鋼鐵流程全生命周期法(LCA)進行能耗評估,考慮鐵料消耗降低4.09kg/t,同時煤氣CO濃度提高3.73%,回收量提高5.57Nm3/t,實現(xiàn)了轉爐煉鋼CO2利用10.08kg/t鋼,噸鋼工序能耗降低6.12kgce,溫室氣體減排26.28kg/t鋼。
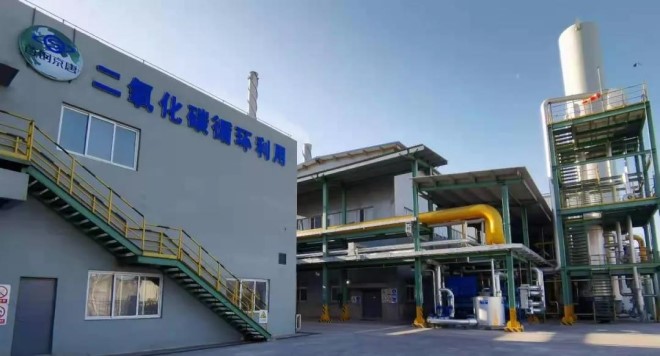
首鋼京唐石灰窯尾氣回收CO2制備凈化工程示范
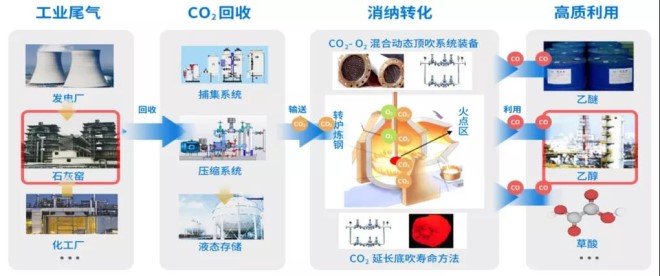
“工業(yè)尾氣→CO2回收→煉鋼利用”的CO2工業(yè)大規(guī)模利用新途徑
作為中國金屬學會重點成果轉化與推廣項目,本項目已在多家鋼鐵企業(yè)成功應用,近三年惠及鋼產(chǎn)量3879.2萬噸,實現(xiàn)工業(yè)CO2利用31.5萬噸,粉塵減少10.3萬噸,爐渣減少24.5萬噸,節(jié)約鋼鐵料增產(chǎn)7.0萬噸,減少脫氧合金用量4500噸。項目實現(xiàn)了煉鋼固廢污染物源頭減量和冶金指標的綜合提升,三年共計節(jié)能20.5萬噸標準煤,實現(xiàn)CO2減排86.0萬噸;煉鋼脫磷、脫氮、控氧效果明顯改善,帶來了顯著的經(jīng)濟及社會效益,三年新增產(chǎn)值4.24億元,增收節(jié)支3.14億元。項目技術可服務于我國80%以上煉鋼產(chǎn)能,實現(xiàn)全行業(yè)大規(guī)模應用。
四項目成果和科技評價
“二氧化碳綠色潔凈煉鋼技術及應用”是項目團隊的開創(chuàng)性研究成果,國內(nèi)外鮮有CO2應用于煉鋼的應用報道。本項目通過對CO2冶金反應特性的研究和利用,掌握了多項顛覆傳統(tǒng)煉鋼技術的工藝方式,取得了顯著的效果。與傳統(tǒng)煉鋼工藝相比,本項目顯著提升了煉鋼技術水平,在終點氮含量、渣中全鐵、終點碳氧積、底吹供氣強度和底吹壽命等指標上全面占優(yōu)。項目共獲發(fā)明專利授權18件、美國、歐盟專利2件,國際PCT專利2件,完成行業(yè)標準5部、出版《二氧化碳煉鋼理論與實踐》專著1部,發(fā)表學術論文66篇。
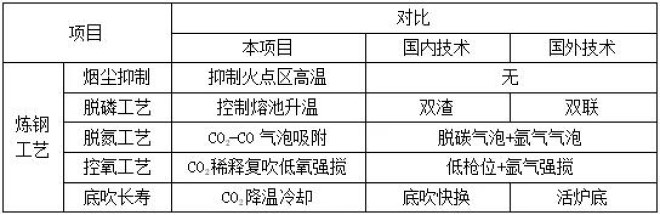
2018年,中國金屬學會組織召開了關于“二氧化碳在煉鋼的資源化應用技術”的科技成果評價會,專家評價委員會一致認為:項目將CO2作為資源應用于煉鋼,減少了金屬的蒸發(fā)及煙塵量,實現(xiàn)CO2煉鋼脫磷、脫氮和控制鋼水過氧化,延長底吹壽命,發(fā)明及理論創(chuàng)新突出,是變廢為寶、一舉兩得的煉鋼新技術,達國際領先水平。
項目已通過工業(yè)和信息化部“原材料工業(yè)20大低碳技術”的第一輪評選,并成功入選了2020年河北省低碳技術推廣目錄?!妒澜缃饘賹蟆贰?018年世界鋼鐵工業(yè)十大技術要聞”指出:該技術首次提出將CO2資源化應用于煉鋼的方法,是一項重大技術發(fā)明,建立健全了CO2煉鋼理論體系,在實現(xiàn)節(jié)能減排及潔凈化冶煉的同時,完成CO2的資源化應用。
本項目示范引領作用顯著,開創(chuàng)了CO2在鋼鐵行業(yè)內(nèi)高質(zhì)化利用的先河,首次形成了鋼鐵行業(yè)CO2資源化利用的標準體系,是溫室氣體CO2利用及減排方法的創(chuàng)新。依托項目成立了“二氧化碳科學研究中心”,形成“產(chǎn)-學-研-用”合作集群,為CO2在全冶金領域擴展利用提供了強力支撐。
本項目作為“中國低碳原創(chuàng)技術”,促進了我國鋼鐵工業(yè)綠色低碳技術的發(fā)展,我國每年將減少煉鋼固體污染物產(chǎn)生1000萬噸,溫室氣體減排2600萬噸,成為建設“碳中和”國家的重要助力,為打贏“藍天、碧水、凈土”保衛(wèi)戰(zhàn)提供了重要技術保障,全面彰顯了“中國創(chuàng)造”對世界鋼鐵行業(yè)節(jié)能減排的突出貢獻。